The Comprehensive Guide to Die Making and Related Processes
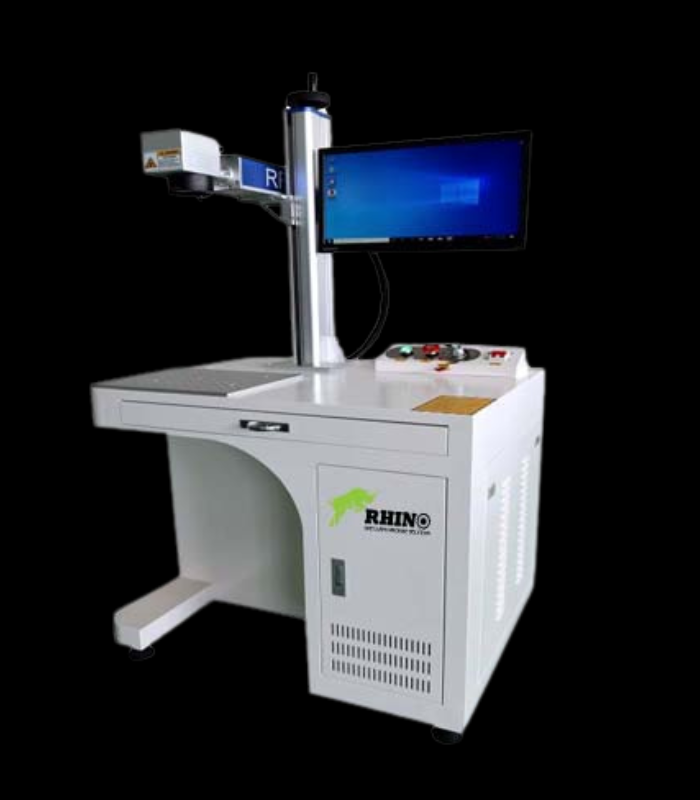
Introduction to Die Making

Die making is a vital process within the manufacturing industry, serving as the backbone for the production of various precision components. This intricate and critical procedure involves creating custom tools known as dies, which are used to shape materials into desired forms. These dies can be employed in processes such as stamping, forging, and molding, where the utmost accuracy and detail are paramount. The significance of die making is underscored by its ability to enhance productivity, facilitate mass production, and ensure consistency across manufactured products.
The die-making process, while complex, can be broadly categorized into several key stages. These stages include design, fabrication, and testing. Initially, a die design is conceptualized, taking into consideration the specific requirements of the production process and the characteristics of the materials to be used. This stage often involves advanced computer-aided design (CAD) software to ensure precision in the dimensions and features of the die. Once the design is finalized, the fabrication stage commences, utilizing various manufacturing techniques like milling, grinding, and electrical discharge machining (EDM) to bring the die from a conceptual stage to a tangible tool.
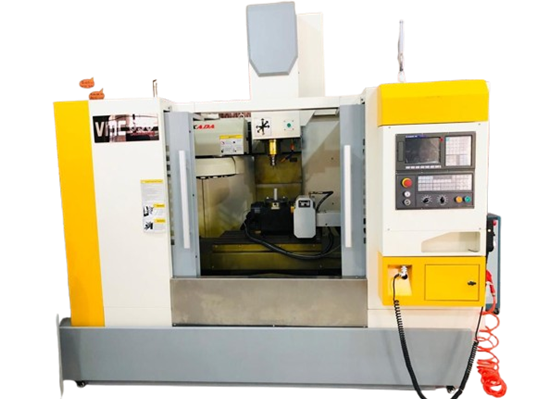
Moreover, the materials used in die making play an equally critical role in determining the effectiveness and longevity of the dies produced. Steel is the predominant choice due to its strength and durability, but other materials such as aluminum and carbide are also used for specific applications. The choice of material often depends on factors such as the production volume, the complexity of the shape, and the type of material being shaped. In essence, a successful die-making process hinges on the harmonious integration of innovative design, precise fabrication, and suitable material selection, ensuring that manufacturers can achieve efficiency and the necessary precision in their production processes.
Understanding Die Cutting
Die cutting is a manufacturing process that utilizes specialized machinery to create shapes from various materials through a precise cutting action. This technique is particularly applied to materials such as special steel sheets, including stainless steel 304, renowned for its durability and resistance to corrosion. The die cutting process involves the use of a die—an industrial tool that cuts various shapes, sizes, and designs efficiently and accurately. The operation typically combines a high-pressure mechanism with a specially manufactured die that forces the material against a cutting edge, allowing for the formation of intricate shapes without wasting raw materials.

One of the significant advantages of die cutting is its ability to produce high volumes of uniform parts at speed, making it an optimal choice for mass production. In addition, the process enhances precision, as the die ensures that each cut is consistent, which is essential for industries that require components to meet strict specifications. Moreover, die cutting minimizes material waste significantly, enabling manufacturers to maximize resource efficiency. The versatility of this technique means it can be applied across a diverse range of industries, including automotive, aerospace, and electronics, where stainless steel 304 parts are often utilized for their mechanical properties and aesthetic appeal.
Industries relying on die cutting benefit from its precision and efficiency. For instance, in the automotive sector, die-cut parts are crucial for manufacturing components such as brackets, guides, and structural supports that not only enhance performance but also contribute to the vehicle’s overall safety. Similarly, in the electronics industry, die cutting allows for the creation of critical parts like shielding and custom enclosures that protect sensitive equipment. By understanding the role of die cutting in these sectors, it becomes evident that this process plays a vital role in modern manufacturing, driving innovation and ensuring quality across various applications.
Raw Material Shearing Techniques
Shearing is a fundamental cutting process utilized in the die making industry to trim or separate raw metal sheets into precise shapes and sizes. This technique employs blades that exert a significant force on the material, enabling clean cuts with minimal deformation. It is an efficient method, facilitating high productivity while maintaining the quality of the finished product.
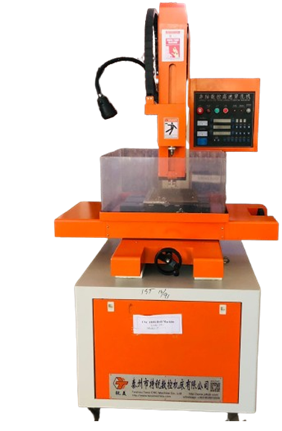
The shearing process operates by positioning the metal sheet between a stationary and a moving blade. As the moving blade descends, it applies localized pressure, causing the material to rupture along a designated line. This technique is crucial in preparing materials for subsequent processing stages, such as stamping, forging, or machining, which often require accurately shaped components for successful operation.
One of the advantages of shearing lies in its speed and precision. Modern shearing machines are equipped with advanced technology that allows for fine-tuning of blade alignment and force application, resulting in minimal waste and reduced scrap material. Additionally, the ability to shear various thicknesses of metal sheets broadens the range of applications, making it suitable for different industries, from automotive to aerospace.
To achieve optimal results in raw material shearing, best practices must be adhered to. Ensuring the blades are adequately maintained and sharp is crucial in preventing material tearing or unwanted burr formation. Furthermore, regular assessments of shear force settings according to the type and thickness of the material being processed are essential for maximizing cutting efficiency. By implementing these strategies, manufacturers can enhance the overall productivity of their die making operations and ensure the integrity of their final products.
The Forging Process Explained
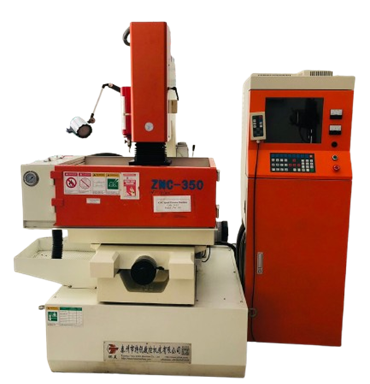
The forging process serves as a fundamental technique in the metalworking industry, employing compressive forces to shape metal into desired forms. This method is paramount for producing components that require high strength and durability, making it an ideal choice for various industrial applications. Forging can broadly be categorized into two types: hot and cold forging, each with its own unique characteristics and benefits.
Hot forging involves heating the metal above its recrystallization temperature, making it more malleable and easier to work with. This process allows for significant deformation of the material without the risk of cracking, producing components with superior mechanical properties. Common applications of hot forging can be found in industries such as automotive, aerospace, and construction, where robust parts like gears, crankshafts, and frames are essential for operational efficiency and safety.
On the other hand, cold forging occurs at or near room temperature. This technique usually results in a higher precision and improved surface finish compared to hot forging. Cold forged components tend to exhibit a greater hardness and tensile strength due to strain hardening. Industries often utilizing cold forging include electronics, fastener production, and precision engineering, where smaller, intricately shaped parts like connectors, screws, and pins are frequently required.
The types of products typically produced via forging encompass a wide array of applications, not limited to fasteners, structural components, and complex machinery parts. Additionally, forging contributes to the grain structure of the metal, enhancing its strength and ductility—a crucial factor in sectors where material integrity is paramount. Overall, the forging process remains an indispensable technique, providing reliable solutions across various industries where performance and durability are key considerations.
An Overview of Machining Methods
Machining is a vital process in the manufacturing sector, serving as a primary method for material removal using various tools. The significance of machining lies in its ability to create precise components that meet stringent specifications. Fundamental machining operations typically include turning, milling, drilling, and grinding, each utilizing specialized equipment such as lathes and milling machines. This accuracy allows manufacturers to achieve tight tolerances, which are crucial for ensuring the functionality and performance of engineered parts.
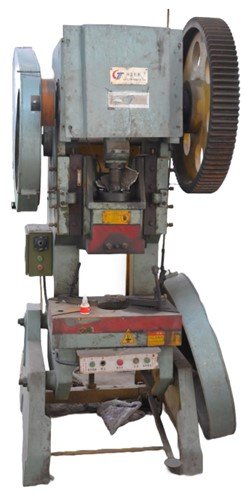
The process begins with the selection of appropriate materials, which can range from metals like steel and aluminum to plastics and composites. Each material responds differently to machining, requiring operators to tailor their techniques accordingly. For instance, harder materials may necessitate the use of advanced tooling and slower feed rates, whereas softer materials can be machined more rapidly. Understanding the characteristics of each workpiece is fundamental for achieving optimal results in machining.
Moreover, modern machining techniques have evolved significantly due to advancements in technology. Computer Numerical Control (CNC) machines represent a major progression in this field, allowing for greater consistency and automation. CNC technology enables manufacturers to produce parts with intricate geometries at a faster pace, reducing human error while increasing productivity. As industries become more reliant on precision-engineered components, the role of machining continues to grow, underpinning the manufacturing processes across sectors such as aerospace, automotive, and medical devices.
In conclusion, machining is a cornerstone of modern manufacturing processes, providing the means to create high-precision parts from various materials. Its continued evolution with the integration of technology promises to enhance manufacturing capabilities, ensuring better quality and efficiency in product development.
The Trimming Process
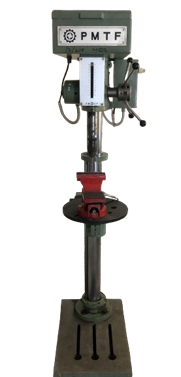
Trimming is a crucial operation in the production of precision dies, where the removal of excess material from parts occurs after initial manufacturing processes such as casting or forging. This step takes on significant importance as it directly impacts the quality and dimensional accuracy of the finished product. The trimming process entails the careful cutting away of any surplus material, which may result from the manufacturing techniques used, to achieve the desired dimensions and surface finishes.
The primary aim of trimming is to ensure that components meet strict specifications in terms of shape and size. During manufacturing, variations can arise due to factors such as tooling wear, material inconsistencies, or fluctuations in the production environment. Hence, the trimming phase becomes essential for eliminating these discrepancies. This not only enhances precision but also reduces the need for further adjustments or corrections later in the production cycle.
Moreover, trimming contributes to the overall aesthetic appeal of the final product. It plays a vital role in detailing, as imperfections or rough edges left from the initial processes can detract from the appearance and functionality of the die. By smoothing out these irregularities, trimming ensures that the components not only perform well but also look polished and professional.
In addition, embracing modern trimming techniques and technologies can bolster workflow efficiency. Automated solutions, such as CNC trimming machines, have revolutionized this process, allowing for higher productivity rates and consistent quality. As manufacturers strive for excellence in die making, the trimming process is an integral part of achieving superior results while minimizing waste and production costs.
Understanding Annealing
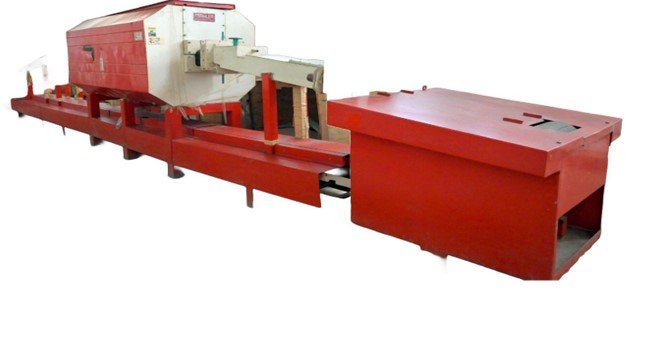
Annealing is a crucial heat treatment process utilized to alter the physical and sometimes chemical properties of a material, effectively enhancing its performance. Primarily used in the metalworking and manufacturing sectors, this technique involves heating metal to a specific temperature and then maintaining that temperature for a predetermined duration before cooling it down slowly. The temperatures utilized in the annealing process can range significantly, typically from 300°C to over 1000°C, depending on the material and desired outcomes.
The primary purpose of annealing is to soften the material, which greatly improves ductility and workability. By modifying the microstructure of the material, annealing reduces hardness and increases the material’s ability to deform under stress, making it more suitable for further processing, such as forging or machining. Additionally, the process alleviates internal stresses that may have developed during prior manufacturing operations, thereby reducing the risk of cracking or distortion in subsequent processes.
Beyond improving ductility, the benefits of annealing extend to enhancing the material’s overall stability and dimensional accuracy. This is particularly important in industries where precision is vital, such as aerospace and automotive sectors. By ensuring that the variables that influence mechanical properties are minimized, manufacturers can produce components that consistently meet stringent performance standards.
The applications of annealing are varied and significant. It is commonly employed in the production of springs, wires, and other components that require high flexibility and strength. Additionally, materials such as steel, aluminum, and copper are typically subjected to annealing treatments to optimize their properties for specific applications. Overall, annealing plays an essential role in the die-making process and many other manufacturing applications, facilitating the production of high-quality components with desirable properties.
Initial Assembling and Filling Techniques
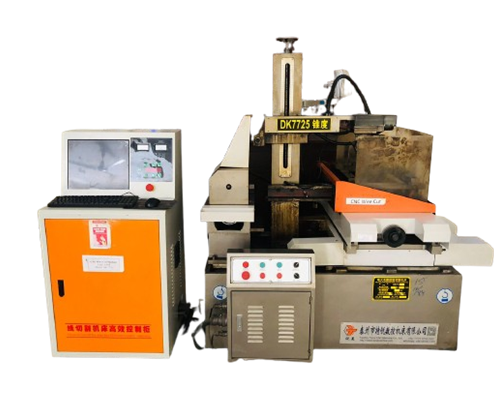
The initial assembling and filling techniques play a crucial role in the die-making process, establishing a foundation that influences the quality and integrity of the final product. A well-executed assembly ensures that all components fit accurately within the mold or assembly fixture, which is essential for achieving uniformity and precision during subsequent operational stages. This section aims to emphasize the methods and best practices for proper alignment and securing of components in various molds.
One of the primary techniques employed in initial assembling is the use of jigs and fixtures. These tools guide and secure the components in place, allowing for precise alignment. For instance, when working with intricate molds, it is pivotal to utilize custom-designed fixtures that accommodate the unique geometries involved. These fixtures not only promote consistent positioning but also facilitate ease of assembly, effectively reducing the likelihood of errors that could compromise product quality.
Another important aspect of filling techniques is ensuring that the materials used are correctly dispensed into the molds. The filling process can vary; for example, a gravity-fed system might be ideal for certain materials, while others may require pressure-assisted filling to prevent air entrapment and ensure comprehensive coverage of all mold cavities. The appropriateness of the filling technique directly impacts the material’s properties and therefore the overall product yield.
Moreover, attention should be paid to the selection of appropriate materials during the filling process. Different materials may react differently under pressure or temperature variations, affecting the assembly integrity and final outcomes. Enhanced monitoring during the initial stages can lead to improved cohesion and adherence within the produced components, setting the stage for efficient machining or further processing.
Heat Treatment Processes

Heat treatment is a crucial technology in the field of metallurgy, utilized extensively for modifying the physical and mechanical properties of metals. This process entails controlled heating and cooling of materials, enhancing characteristics such as hardness, strength, ductility, and corrosion resistance. The fundamental principle lies in altering the microstructure of metals to achieve desired performance attributes tailored to specific applications.
There are several methods of heat treatment, each serving unique purposes. Annealing is one of the most common techniques, which involves heating the metal to a specific temperature and then cooling it slowly. This process is primarily used to relieve internal stresses, increase ductility, and refine the grain structure. Quenching, another vital heat treatment process, involves rapid cooling of a hot metal, typically in water or oil. This method enhances hardness but may introduce brittleness. Tempering, which follows quenching, entails reheating to a lower temperature to reduce brittleness while maintaining sufficient hardness.
Additionally, processes such as normalizing and hardening are also noteworthy within this domain. Normalizing addresses the non-uniform structure and stress in metals, enhancing their mechanical properties by air cooling after heating to a high temperature. Hardening often applies to tool steels where improving wear resistance is essential. Each of these heat treatment techniques conforms to specific industry standards, which ensure consistent quality and reliability in metal performance.
In aerospace, automotive, and manufacturing industries, the application of heat treatment processes is vital for producing durable components that can withstand harsh operational environments. Understanding various heat treatment processes is essential for metallurgists and engineers as they play an instrumental role in selecting the appropriate method to enhance metal qualities for their specific applications.
Electropolishing and Surface Finishing
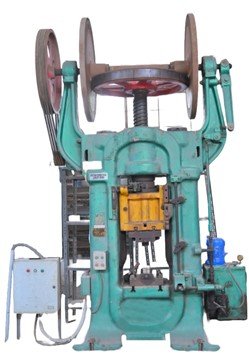
Electropolishing is a crucial process in the die-making industry, specifically designed to improve the surface finish of metal parts. This electrochemical method involves the removal of material from the surface of a workpiece, primarily to enhance its finish. By applying a controlled electrical current in a suitable electrolyte solution, the high points of the surface are removed preferentially, resulting in a smoother, more polished finish. This process not only increases the aesthetic appeal of the metal components but also enhances their corrosion resistance—critical factors in various applications, particularly in environments prone to moisture and chemical exposure.
In addition to electropolishing, various surface finishing techniques are employed to achieve desired results. Grinding is one such method that utilizes abrasive materials to refine and smooth surfaces. It is commonly used in preparing dies to ensure precise dimensions and surface properties. Polishing, typically following grinding, uses finer abrasives or polishing compounds to create a reflective finish. Both methods, when properly executed, contribute significantly to the overall functionality and longevity of the metal parts.
The significance of achieving a clean, polished finish cannot be understated. A smooth surface enhances the performance of the die by reducing friction during the manufacturing process and minimizing the likelihood of defects in the final products. Furthermore, a polished surface can impede the adherence of contaminants and help prevent corrosion, thereby prolonging the life of metal components across a range of applications.
Ultimately, the integration of electropolishing, grinding, and polishing techniques is essential in the die-making process. These methods not only support the mechanical performance of a component but also ensure that it meets the high standards often required in the manufacturing industry.